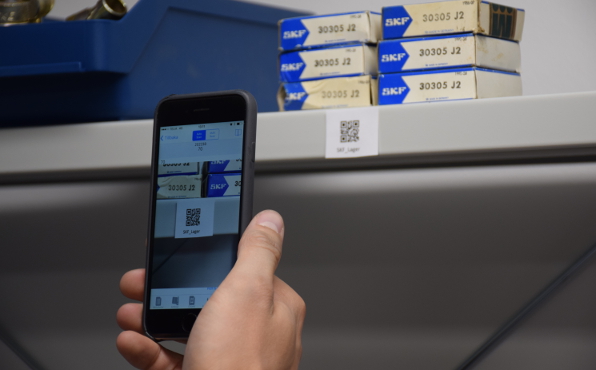
A very important function of the maintenance system is to reach a high level of balance security. In the worst case spare shortage can result in unnecessary long downtime which in addition will lead to delayed deliveries and reduced profitability. Always having every spare part in stock however is not possible because it would tie up way to much capital in the maintenance store. That’s why it is important to work with reminders and order points. When the material have been withdrawn by a digital withdrawal the system will remind us that it is time to order new material.
In order for the system to give us reminders of what and who we need to order something from, we need to take do these digital withdrawals. There are several simple ways to make withdrawals and they are also easy to carry out regardless of computer experience.

Withdrawals
It will only take a few second to withdraw material with the app. You can either search for the material or scan the barcode or QR-code on the shelf. Choose and amount and withdraw. Another common solution is leaving a smartphone or a handheld computer in the store and manage your withdrawals with it.
Larger companies often have responsible store personnel who manages the balance security. Store personnel are desktop bound and stationery in the store. When material is to be withdrawn the store personnel will deduct the material and submit the material to the technician. Withdrawals can be also be automatically made when the work order is closed.

Indeliveries
When the material has arrived, it is easy to make an in delivery. The in delivery is either made by the app, the handheld computer or from the desktop application. You can add the material one by one or by creating a list and import the list right away.

Returns
If something goes wrong with the in delivery or if the material wasn’t consumed you can always undo by creating a return. The material will then be returned directly to the inventory balance.

Stocktacking
Stocktaking doesn’t need to be exhausting or time consuming. With the app or a handheld computer, you can efficiently scan the material, insert the amount that you see on the shelf and move to the next storage place.

Order points
When the material has reached its order point you will get a remind that you need to order more material. You can also add lead times and reminders on reoccurring planned maintenance so that you in advance can order your material when the planned maintenance activity is approaching.