Hem » Idus Maintenance System
Maintenance System
Idus Maintenance System helps you plan, follow up and improve maintenance together, regardless of what your goals are or where you start from.
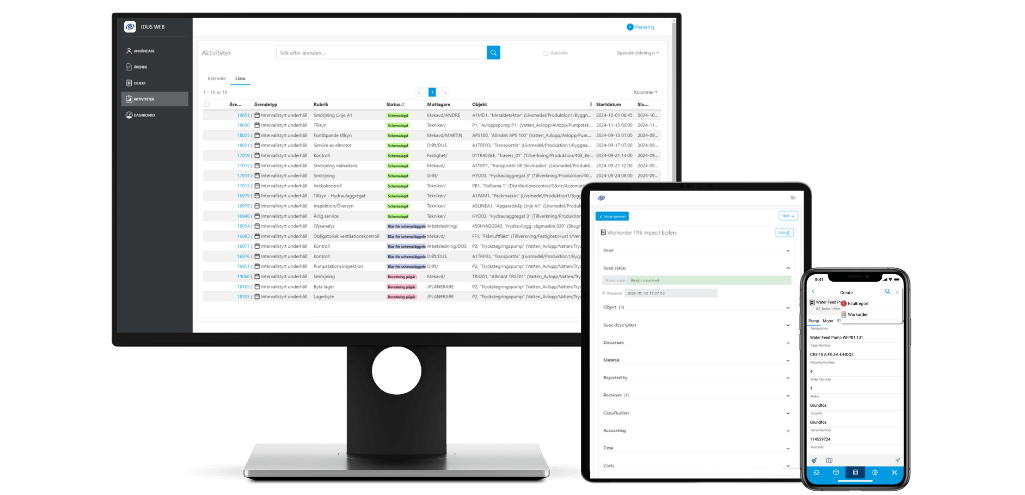
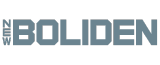
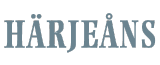
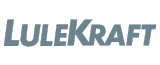
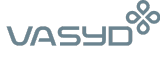
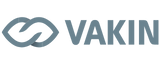
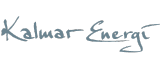
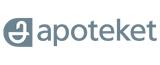
Explore how Idus Maintenance System creates control
An activity list in the maintenance system where all work orders are located
When planning, it is important to be able to easily overview which works need to be carried out, how they must be carried out and with what materials. Idus collects all information about the plant, associated spare parts and history from previous work.
Before the job is to be carried out, you have plenty of time to plan and schedule the work. You can view all calendars and
the craftpeople’s occupancy, which makes it easier to administer the work order backlog. Even if you outsource a lot of maintenance work, you can distribute the jobs by sending work orders to external emails.
Idus gives you the conditions to get maximum benefit from the maintenance warehouse. You get a quick overview of what needs to be ordered, which quantities and from which suppliers. Idus provides support through the entire purchasing process from request to certificate and purchase order. You can also email the supplier directly from the system.
As a maintenance manager, it is important to have access to a wide range of statistics and reports. Idus contains over 100 reports that provide important insights into maintenance operations and the status of the facility. Examples of reports can be schedule compliance, carried out work, distribution of maintenance type and key figures.
Maintenance in
your phone or tablet
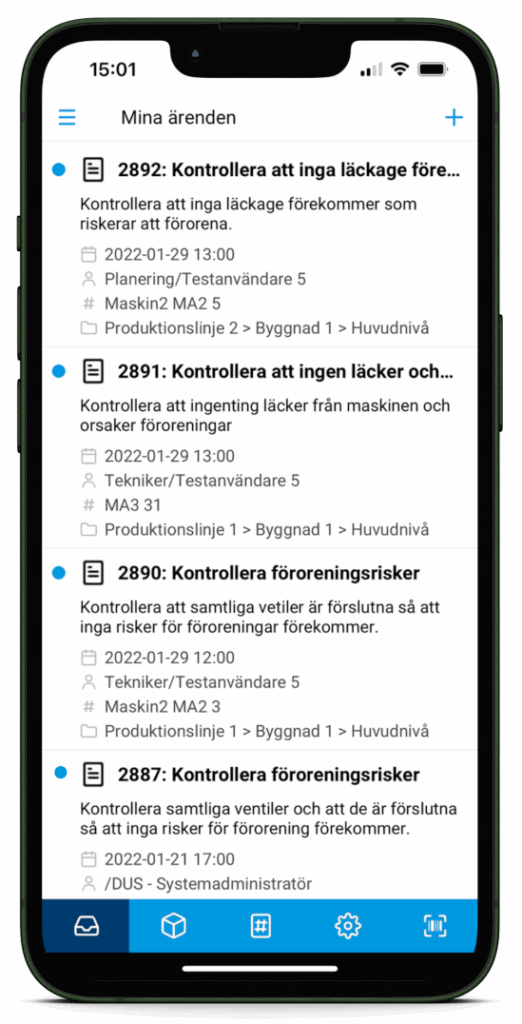
Create activitites
Even when working in the plant you can create work orders and requets.
Close work orders
Close work orders and report useful information like worked hours, material, fault causes, etc.
Look at machines
Wherever you are you can always access your entire plant, documents and previous jobs directly in your smartphone or tablet.
Withdraw material
Complete control over your store and available spare parts doesn’t need to be hard. Idus makes it easy to manage spare parts.
What can better maintenance bring?
Based on results from real maintenance organizations
Using a maintenance system can reduce
total maintenance costs by at least 10%.
By improving maintenance procedures, you can reduce maintenance costs by 20%.
Better documentation and planning of maintenance activities can cut lead times in half.
We will get you started
Get your maintenance system up and running right away with a five-day starter package. Together, we start the most important modules for you and adapt them to your business.
We will get you started
Get your maintenance system up and running right away with a five-day starter package. Together, we start the most important modules for you and adapt them to your business.
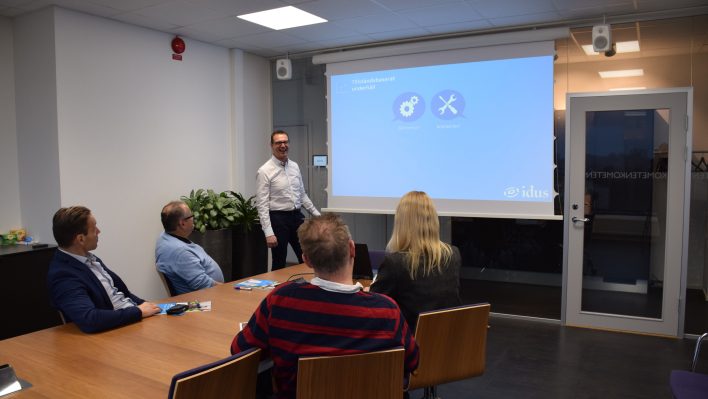
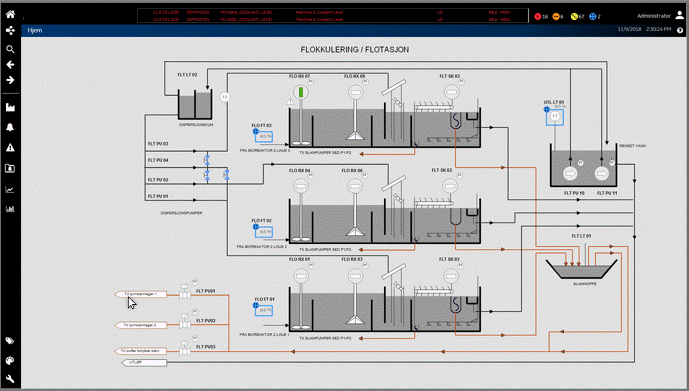
SCADA system
- Right-click in your SCADA
- Receive fault reports on alarms
- Get work orders on operational data
With Idus SCADA integrations, you reach Idus commands by right-clicking on the points in your HMI/SCADA.
Idus will retrieve signals from all HMI/SCADA. ready made-functions will connect Idus and your SCADA and base maintenance intervals on actual machine usage. Condition-based maintenance can quickly saves resources and increases availability.
What our users say:
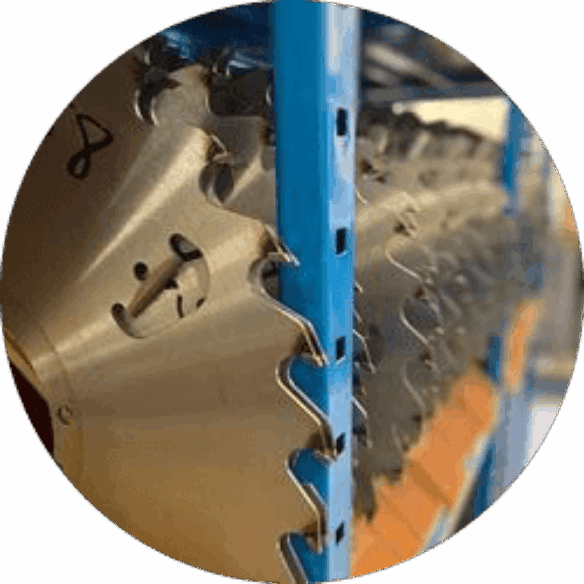
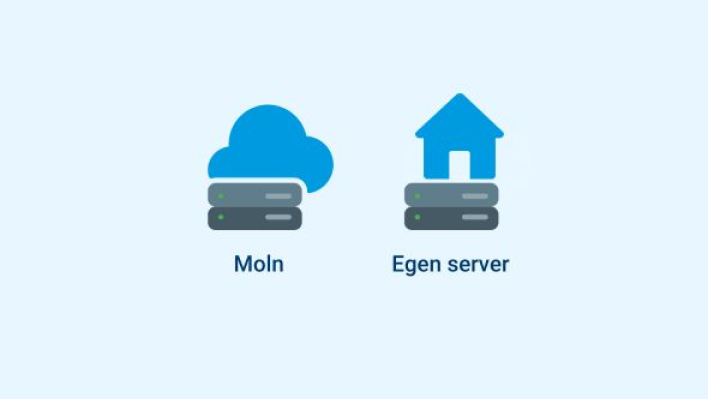
Safer hosting
You can run Idus completely in the cloud with only a browser as access or you can store Idus safely on your own server, whatever suits your internal IT policy.
Safer hosting
You can run Idus completely in the cloud with only a browser as access or you can store Idus safely on your own server, whatever suits your internal IT policy.
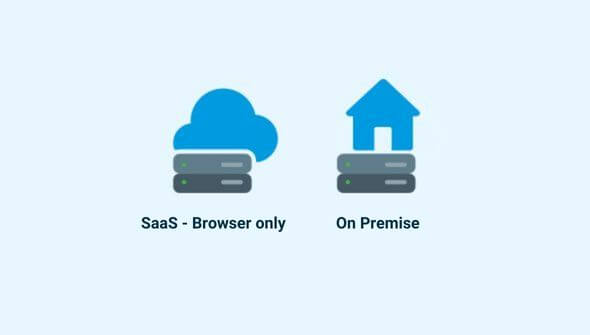
Book a demo
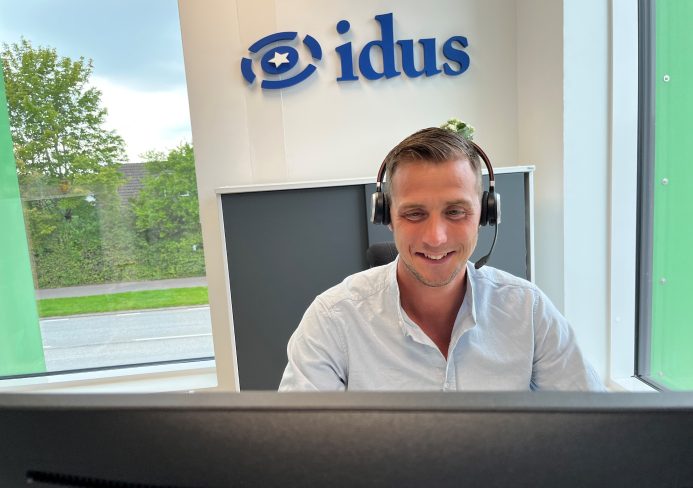
Frequently asked questions
A maintenance system is a software company uses to be able to plan, follow up and improve maintenance operations. Also called CMMS, Computerized Maintenance Management System or EAM System – Enterprise Asset Management System.
Companies with recurring maintenance work and which depend on the technical operation to function use maintenance systems to ensure that the maintenance is carried out at the right time so that the operation avoids unplanned costly stops.
It is best if everyone in the business uses the system. Different roles use different parts of the system. From filing an error report to analyzing statistics and reports.
Once the software is downloaded, it typically takes between one and five days to deploy the facility, create recurring jobs, and launch the system, depending on the complexity and level of detail. A good rule of thumb is to always start as simple as possible.